- در این جلسه مورخ 27 تیرماه ۱۴۰3 بررسی حلقه کنترل خوراک فیلترهای فشاری مجتمع مس سرچشمه برگزار گردید که به معرفی مدار آبگیری کنسانتره مس، معرفی اجزا فیلترهای فشاری، خوراکدهی به فیلترهای فشاری، حلقه کنترلی فشار خوراک فیلترفشاری و اهمیت آن، موانع و راه حل رفع عیب از حلقه کنترلی فشار خوراک پرداخته شد.
معرفی مدار آبگیری کنسانتره مس
تیکنرهای مس مجتمع سرچشمه با باطله کارخانه مولیبدن که همان کنسانتره مس است ، خوراک دهی می شوند . تیکنرهای مس شامل تیکنرهای شمال و جنوب ( طرح قدیم ) و تیکنرهای ۳ و ۴ ( طرح توسعه ) که باطله کارخانه مولیبدن ابتدا به یک مقسم کلی ارسال می شود و سپس به ساختمان انتقال تیکنرهای شمال و جنوب و ساختمان انتقال تیکنرهای ۳ و ۴ منتقل می شود. .
تیکنرهای مس طبق طرح با ۱۵ درصد جامد خوراک دهی می شوند و با ته ریز 50 درصد جامد تیکنرهای شمال و جنوب به ساختمان فیلتر خلا دیسکی و ته ریز 65 درصد به تیکنرهای مس ۳ و۴ به ساختمان فیلترفشاری ارسال می شوند..
ساختمان فیلترهای دیسکی شامل سه عدد فیلتر که از تیکنرهای شمال و جنوب به دو فیلتر طبق طراحی خوراک دهی میشود و کیک فیلتر با رطوبت 14-18 درصد به یک خشک کن وارد میشود و در نهایت محصول خروجی خشک کن با رطوبت 7 درصد طبق طرح روی نوار 20 ریخته شده و به انبار کنسانتره ارسال میگردد(شکل1).
شکل1 – شمای مدار آبگیری کنسانتره مس مجتمع سرچشمه
آبگیری با فیلترهای فشاری
فیلتراسیون با استفاده از فیلترهای فشاری یکی از روشهای مؤثر در جداسازی مواد جامد از مایعات در صنعت فرآوری مواد معدنی میباشد که با توجه به کاهش هزینه برای مصرف انرژی و محیط زیست فیلترهای فشاری برای آبگیری مواد، مهمی ایفا میکنند. این فیلترها شامل سطحی متخلخل (پارچه) هستند که با ایجاد اختلاف فشار در دو طرف این سطح، آب موجود در پالپ از آن عبور کرده و ذرات جامد به صورت کیکی بر روی آن باقی میمانند.
عمل آبگیری فیلترهای فشاری مطابق شکل 2 به صورت یک سیکل از مراحل زیر تشکیل شده است:
- آبگیری با استفاده از فشار پمپ خوراکدهی
- فشار و به اصطلاحاً چلاندن کیک تشکیل شده بین پارچهها توسط باز شدن ممبران یا غشا
- افزایش آبگیری با استفاده از دمیدن هوای فشرده که جایگزین آب محبوس بین کیک و همچنین تبخیر بخشی از آن
شکل2- نمودار مراحل آبگیری با فیلترهای فشاری
اجزا فیلترهای فشاری
پارچه فیلتر، نقش جداکردن آب از مواد را به عهده دارد و نازلها نیز فضای بین پارچهها را شستشو میدهند. پارچهها به طور معمول بین 4000 تا 4500 دوره کاری عمر دارند. اما عواملی مانند خراب بودن صفحات، معیوببودن لاستیک آببند خوراک، شستشوی نامناسب و یا عدم پرشدگی کامل فضای بین پارچهها توسط خوراک میتواند عمر آنها را کاهش دهد. شکل3 نمایی از محل قرارگیری دوشهای آب شستشو و محل ورود خوراک بین پارچه فیلترها را نشان میدهد.
شکل3- نمایی از پارچهها و نازلهای شستشو
هر جفت پارچه فیلتر که روی یک نازل قرار میگیرند، ازیکطرف به صفحات فیلتر و از طرف دیگر به صفحات با غشای لاستیکی متصل شدهاند. زمانی که جکها جمع میشوند و صفحات و پارچهها را جمع میکنند، چندین لوله مجازی تشکیل میشود که از لوله مرکزی خوراک، بین پارچهها قرار میگیرد و پس از طی مراحل مختلف فیلترکنی به کیک تبدیل میشود. شکل4 نمایی از نحوه قرارگرفتن پارچهها، صفحات ممبرانها و صفحات فیلتر نشان میدهد.
شکل4- نمایی از صفحات فیلتر، پارچهها و صفحات ممبران
خوراکدهی به فیلترهای فشاری
فیلترهای فشاری به طور معمول با پمپهای سانتریفیوژ یا جابهجایی مثبت خوراکدهی میشوند. که یکی از عواملی که خوراکدهی به فیلترها مورد توجه است، فشار خوراک به آنها میباشد. هرچه فشار خوراک بیشتر باشد باعث فشردگی بیشتر کیک میان پارچه فیلترها شده و موجب آبگیری بیشتر از آن میگردد اما استفاده از پمپها در اعمال فشارهای بالاتر محدودیتهایی را ایجاد کرده است.
برای خوراکدهی فیلترهای فشاری مجتمع مس سرچشمه از پمپهای سانتریفیوژ (گریز از مرکز) استفاده میشود که مطابق شکل 5 خوراکدهی با پمپ گریز از مرکز تا یک حدی در بازه زمانی افزایش مییابد و همزمان با این این افزایش فشار کاهش دبی را در پی دارد.
شکل5- نمودار فشار و دبی خوراکدهی با پمپ گریز از مرکز بر حسب زمان
با توجه به نوسان ها در کارخانهها و عوامل تاثیر گذار بر فشار در پمپهای سانتریفوژ می توان به دانسیته خشک ذرات، ابعاد ذرات و درصد جامد پالپ اشاره کرد که با افزایش مواد ذکر شده در یک دبی یکسان، فشار اعمال شده با پمپ کاهش مییابد که بایستی به این موارد در خوراکدهی و انتخاب پمپ مناسب توجه شود.
خوراکدهی به فیلترهای فشاری مجتمع سرچشمه بر اساس دو الگو زیر انجام میشود:
- زمان-وزن:
زمان خوراکدهی و حداقل وزنی که بایستی بارگیری شود توسط اپراتور تنظیم گردیده و پس گذشت زمان تنظیم شده و سنجش وزن بارگیری شده توسط لودسلهای فیلترهای فشاری انجام شده و با شرط وزن مقایسه میکند که در صورت رسیدن به شرط وزن به مرحله بعدی سیکل میرود و در صورت عدم تایید شرط وزن مجددا بارگیری بر اساس زمان انجام میشود.
- فشار-وزن
فشار خوراکدهی و حداقل وزنی که بایستی بارگیری شود توسط اپراتور تنظیم گردیده و پس گذشت رسیدن به فشار و سنجش وزن بارگیری شده توسط لودسلهای فیلترهای فشاری انجام شده و با شرط وزن مقایسه میکند که در صورت رسیدن به شرط وزن به مرحله بعدی سیکل میرود و در صورت عدم تایید شرط وزن مجددا بارگیری بر اساس زمان انجام میشود.
کنترل تنظیم فشار خوراک فیلترهای فشاری
کنترل فشار خوراک در فیلترهای فشاری به صورت انجام میشود که یک فشارسنج در مسیر خوراکدهی به فیلتر وجود دارد که پس از اندازهگیری فشار و مقایسه فشار با مقدار تنظیم شده در صورت اینکه مقدار اندازه گیری به مقدار تنظیم شده رسیده باشد به پمپ خوراکدهی دستور قطع ارسال میشود(شکل6).
شکل6- شمای سیستم کنترل فشار خوراک فیلتر فشاری
استاده از این کنترل فشار خوراک از جهات مختلفی داری اهمیت است که میتوان به موارد زیر در این خصوص اشاره نمود:
- افزایش آبگیری در بخش خوراک دهی با استفاده از فشار مطلوب
- افزایش تناژ فیلتر در اثر افزایش فشار
- عدم نیاز به تعیین زمان بندی خوراک دهی فیلتر توسط اپراتور
- کاهش زمان استفاده از هوای فشرده برای آبگیری
- کاهش خرابی و اسهلاک پمپ خوراکدهی
موانع راه اندازی کنترل فشار خوراک فیلترهای فشاری
استفاده صحیح از هر تجهیز قطعا با یک سری از چالشها و موانع رو به رو خواهد بود که برای رفع عیب آنها بایستی در ابتدا علتیابی شده و در مرحله بعد برای رفع عیب از آن بایستی اقدامات لازم انجام شود. برای راه اندازی کنترل فشار خوراک بررسیهای میدانی برای شناخت چالشها و موانع استفاده از آن انجام شد که در ادامه به آنها پرداخته میشود.
یکی از چالشهای راه اندازی این کنترل استفاده کارکرد فیلترهای فشاری با درصدجامد پالپ خوراک متفاوت نسبت به درصد جامد طراحی این تجهیز میباشد. همانطور که ذکر شد، درصدجامد با فشار رابطه معکوس دارد و با کاهش درصد جامد خوراک بایستی مقدار فشار مطلوب در سیستم کنترل فشار توسط اپراتور بیش از فشار طراحی گذاشته شود. در شکل7 نوسان Bedmass تیکنر مس 4 را نمایش میدهد که در بازه 86 تا 12 درصد در حال نوسان است که میانگین آن 49 درصد میباشد.
شکل7- Bedmass تیکنر مس 4
برای سنجش فشار خوراک بایستی از فشارسنج با دیافراگم که با عنوان واسط بین پالپ و فشارسنج باشد تا از خرابی فشارسنج جلوگیری شود. پس از نصب فشارسنج و پایش آن ، در ابتدای نصب بارگیری فیلترفشاری 8300 کیلوگرم انجام شد اما پس از گذشت چند روز از نصب در فشار یکسان بارگیری از 2100 کیلوگرم تجاوز نمیکرد و موجب عدم استفاده توسط اپراتور از کنترل فشار خوراک و مجددا از الگو زمان – وزن استفاده میشد. پس از بررسی ها ، به علت رسوب گرفتن مواد زیر دیافراگم فشارسنج موجب سنجش فشار بیش از مقدار واقعی شده و در روند بارگیری فیلترفشاری برای تامین وزن مطلوب کیک اخلال ایجاد میکرد(شکل8).
شکل8- رسوب گرفتن زیر دیافراگم فشارسنج
از همین رو جهت یافت راه حل مناسب برای رفع چالش مذکور، بررسیها و بازدید از سایر انواع فیلترهای فشاری انجام شد که در نهایت تصمیم به تغییر دیافراگم فشارسنج از دیافراگم تخت به دیافراگم Isolation Ring گرفته شد. همچنین بازدید و بررسی فیلترهای فشاری کارخانه مولیبدن مجتمع مس سرچشمه از صحت عملکرد این نوع دیافراگم اطمینان حاصل شد. از مزیتهای مهم استفاده از این نوع دیافراگم بالاتر بودن دقت اندازهگیری فشار و همچنین در قرار گرفتن در مسیر پالپ بوده که در هر سیکل در مرحله شستشو مسیر خوراک این دیافراگم هم شستشو داده میشود و از رسوب گرفتگی آن جلوگیری میشود(شکل9).
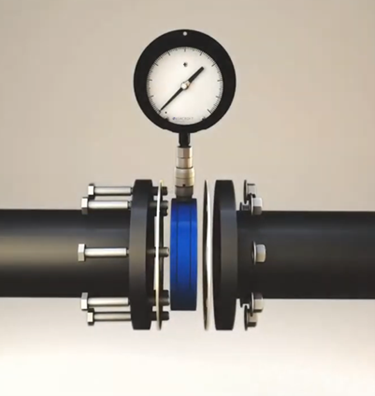
الف)
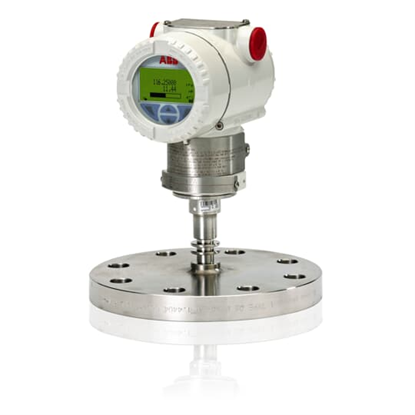
ب)
شکل9- الف) فشارسنج با Isolation Ring ب) فشارسنج با دیافراگم تخت